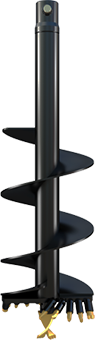
RC4 Combination Auger
RC4 Combination Auger
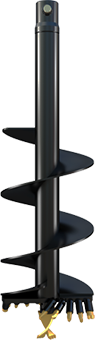
Durability, versatility, and ease of use
With over 40 years of expertise in auger design, Digga’s RC4 augers are crafted for efficient drilling in challenging conditions. Equipped with a narrow cutting head and MFT tungsten carbide teeth, the RC4 allows for superior penetration in hard ground while still performing well in softer soils and clays. Its heavy-duty centre shaft and double-start, single-carry flight configuration enhance spoil removal, making it versatile across a wide range of terrains—from soft soils to shale and hard rock. This combination design bridges the gap between general-purpose bladed augers and dedicated rock augers, offering reliable performance in nearly all drilling conditions.
If your drilling requirements differ from the capabilities of the RC auger, explore our Earth, and DR (Dedicated Rock) augers, or consider a custom drilling solution. Our experienced drilling specialists are ready to help you find the perfect tool for your specific needs. Discover custom augers tailored to your applications.
Other Models Available
Ground Conditions
Drive Compatibility
Machine Suitability
Finishes Available
Warranty
Jump to:
Specifications
Jump to:
Operator’s Manuals
Jump to:
About Augers
Jump to:
FAQs
Features
Effective. Performs reliably across a broad spectrum of ground conditions. with an extensive range of sizes, and extensions to meet various needs.
Durable. Built with robust construction to ensure longevity and maximise return on investment.
Reliable. UK-made, purpose-built for trouble-free performance, delivering consistent satisfaction.
Intuitive. The ‘Taper-Loc’ knock-in-&-out tooth system is designed for effortless operation, requiring only a tapered pin punch, and copper-faced hammer to install and replace.
Specifications
Digga Augers are designed in multiple configurations, to accommodate a wide range of drilling requirements. Refer to the information below to help with selecting the right auger series for your specific needs. If you need further assistance, don’t hesitate to reach out. Our knowledgeable team is here to help with quotes, orders, product details, and any general enquiries.
Drive Suitability | PDD to PD4 |
Machine Size Suitability | Up to 5T |
Ground Conditions | General soils / Sandy loam / Clay / Compacted soils / Shale / Rock |
Hub | 65mm Round |
Hub (Optional) | 50.8mm Round / 50.8mm Hex / 57mm Square / 75mm Square |
Overall Length | 1200mm |
Tooth Type | Multi-faceted tungsten (MFT) TT Series |
Pilot Type | Hex drive / Fishtail multi-faceted tungsten (MFT) |
Tooth Options | 3 (See wearparts) |
Available Range | 150mm to 600mm |
---|---|
150mm | 500mm |
200mm | 600mm |
225mm | 750mm |
250mm | 900mm |
300mm | 1000mm |
350mm | 1200mm |
375mm | 1500mm |
400mm |
Tooth Type | Taper-fit / MFT (Multi-faceted tungsten) |
Pilot Type | Hex drive / Fishtail multi-faceted tungsten (MFT) |
Body Configuration | Double start with single carry flight |
Suits Tough Varied Conditions | General earth / Clay / Shale / Fracturable rock |
Auger Teeth
The RC4 Earth/Rock Combo augers are equipped with two types of durable tungsten carbide teeth for optimized performance. The outside/gauge tooth, featuring a double multi-faceted tungsten (MFT) Taper-Loc design, provides full pocket protection and strong cutting power. The inside/chisel tooth is designed for effective ripping in fracturable ground. Both teeth use Digga’s Taper-Loc retention system for quick installation and removal, with a simple knock-in/knock-out process. This system, compatible with TTD-H auger pockets, only requires a tapered pin punch and a copper-faced hammer.
Tooth Configuration
For general ground conditions, we suggest pairing double tungsten (outside) teeth with single tungsten chisel (inside) teeth. The double tungsten teeth accurately cut the diameter while shielding the flights and pockets, and the inner chisel teeth work well to fracture and break up the ground. In sticky clay or non-fracturable soils, an all-double tungsten carbide tooth setup is ideal. The double teeth slice through clay more effectively, providing extra width for improved pocket protection and grinding capability in hard soils, resulting in a cleaner finish.
Auger Pilots
The RC4 auger features a hex-drive fishtail-style pilot, offering greater reliability than threaded, screw, or lug-style drives. Hex-fit pilots are more durable and can be easily replaced when worn. The fishtail design helps pull the auger into the ground, making it especially useful for lower-tonnage host machines.
X4 Auger extensions
Digga’s drilling extension range is the ultimate in quality and cost effectiveness. Our extensions are manufactured in-house by Digga using only the highest grade materials and strictest quality control. The X4 range of extensions is suited for machines up to 5 tonnes.
Specifications
Maximum Torque: 4200Nm
Standard Hub: 65mm Round
Body (Diameter x Wall): 75mm x 7.5mm
Lengths: 500 / 800 / 1000 / 1500mm
MY.DIGGA.COM
Find everything you need for your Digga attachment – Including operator manuals, safety information, risk assessments, electrical guides, maintenance tips, and ‘how to’ instructions. Our user-friendly interface and easy navigation ensure that you can quickly access the support and information you need.
LEARN MORE ABOUT AUGERS
Explore various types of augers, their components, and maintenance tips to enhance your knowledge and optimise your equipment. We hope you find this information valuable and informative.
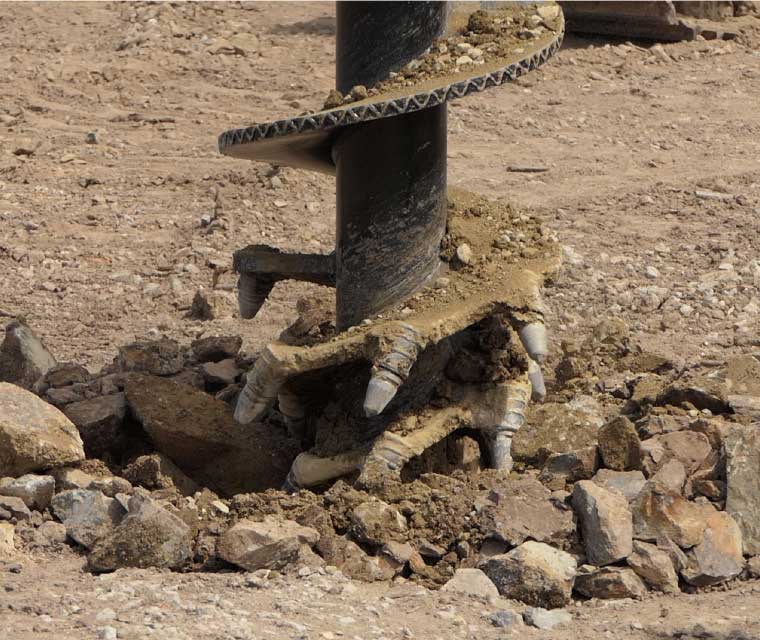
FREQUENTLY ASKED QUESTIONS [FAQS]
Do you make an Auger to drill hard rock?
Yes, we manufacture augers that are specifically designed to drill through hard rock. – Dedicated rock augers, Tapered rock augers, Rock Combo augers, Core Barrels, Drilling buckets and custom solutions.
These augers, often referred to as rock augers, or rock drilling tools, have special features that allow them to handle the high levels of wear and tear that come with drilling through hard rock. Some of these features include.
Tungsten Carbide Teeth are designed to be extremely hard and durable, able to withstand the rigors of drilling through hard rock. They can be replaced when they wear out.
Rock augers are typically made with heavy-duty materials that are designed to withstand the high forces and stresses that come with drilling through hard rock. Typically, with addition of hard facing on common wear areas to assist in additional life of the auger.
It's important to note that drilling through very hard rock can be a difficult and time-consuming process and may require the use of specialised drilling equipment, not supplied by Digga like rotary drills or diamond-tipped core drills.
**The ability to drill rock it also very dependent on the host machine size, by fitting a rock auger won’t guarantee you’ll be able to penetrate all rock.
It comes down to the combination down pressure generated from the host machine together with the type of drilling tool and ultimately the MPA (Hardness) of the rock.
For example, a 2t excavator fitted with 450mm dedicated Rock auger, drilling into 250Mpa rock will be unsuccessful, as the down pressures generated from the host machine is not greater than the strength of the rock there for the rock will not fracture meaning the only way to remove the rock will be by grind it away, this will be very time consuming and could use a large amount of wearparts, so in most cases is uneconomical.
What’s the hardest rock I can drill?
The hardness of rock can vary greatly, and different types of rock will require different types of drilling equipment and techniques to drill through. Some of the hardest rocks that can be drilled include:
Granite: Granite is a type of igneous rock that is known for its high density and hardness. It is composed mainly of feldspar and quartz, which are both very hard minerals. Drilling through granite typically requires specialist drill bits and a great deal of time and effort.
Basalt: Basalt is a type of volcanic rock that is also known for its high density and hardness. It is composed mainly of plagioclase feldspar and pyroxene and can be difficult to drill through.
Quartzite: Quartzite is a type of metamorphic rock that is composed mainly of quartz. It is extremely hard and durable, making it difficult to drill through.
Each of these types of rock and with all types of ground conditions they are found in varying forms of hardness the lower the hardness the better chance of drilling it you will have.
As a very general guide and with the right host machine you could expect to see:
- Using a RC auger in the range of ~10 to 80MPa
- Using a DR auger in the range of ~50 to 150MPa
- Using a TR auger in the range of ~50 to 200MPa
- Using a rotating pick Core Barrel in the range of ~50 to 250MPa
- For any rock over ~90Mpa you would typically need a 20t host machine to succeed
It's important to note that drilling through these rocks and other hard materials may require specialized equipment, and also require the use of fluids or coolants to reduce heat and wear on the drill bits.
Additionally, the drilling process may take a longer time and require more effort than drilling through softer materials.
When should I use a tapered rock auger and core barrel?
These types of drilling tools are typically used when the rock being drilled is of high strength or hardness and are additional tools to assist in trying to penetrate the rock.
A tapered rock auger is a type of auger that is specifically designed for drilling through hard rock and other difficult ground conditions. They typically have a tapered design, meaning that the diameter of the auger gradually increases from the centre out until it reached full diameter assisting in creating wear spots in the rock material in an attempt to break or fractur the rock away. Tapered rock augers should be used in situations where the soil or ground is hard, rocky, or otherwise difficult to dig through. They are ideal for drilling through tough materials such as granite, limestone, and basalt, and are also well suited for drilling through mixed soil conditions that include rock or boulders. They are often used in combination with a Dedicated rock auger, whereby the operated alternates between the two tools to achieve penetration. Example: start with Dedicated rock (DR) if you experience refusal, swap out the DR for a Tapered Rock (TR) this should help penetrate the rock, should the TR then get refusal swap back to the DR and continue the process.
It's important to note that tapered rock augers are typically more expensive than standard augers and may also require more powerful equipment to operate. They also may not be appropriate for certain types of projects where the ground is mainly soil or you require a flat base at the bottom of the hole. (you would use the DR to achieve the flatter base)
A core barrel is typically used on very hard rock where a DR or TR auger is getting refusal in theory it achieves penetrating by having less rock to drill away or break up, it cuts a ring around the rock leaving a core in the centre this requires less power and less down force to achieve the downside of this is the ability to break off the core and remove it from the hole. This application is very hard on the auger drive and can generate huge side loads if not done correctly, and wont work in all ground conditions.
Can I put rock teeth on my earth auger?
Yes, if the auger is the A4TL, A6 or A8 series, you can. The Earth cutter (teeth and Pilot) can be removed and replaced with Tungsten Carbide Cutters (teeth and Pilot).
The tungsten carbide cutters come in two types: a TC version which is a flat tungsten carbide tile or the more aggressive MFT which is a Multifaceted tungsten carbide tile.
The MFT and TC Rock wearparts (teeth & Pilot) are designed to help an auger cut through harder, more difficult soils and materials, such as shale, “soft rock” and hardpan sub soils.
They are made utilising tungsten carbide tiles fitted to the tooth body. When fitting these wear parts to the cutting head it improves the augers’ ability to dig through tough materials.
Fitting rock teeth on an earth auger can increase its versatility and allow it to be used in different types of ground conditions, however, it's important to keep in mind that earth augers are typically not as heavy-duty as dedicated rock augers and may not be able to handle the same level of wear and tear that traditional rock augers can.
It's also important to note that when using rock teeth on an earth auger, make sure that the teeth are properly installed and securely fastened, and to regularly check and maintain the teeth to ensure they are in good condition. When drilling in harder ground or rock/rocky ground typically the wear will be extreme when compared to soil drilling.
Consult with the sales or spare parts team for available options and guidance to help you make the best decision.
What size Augers should I buy for fencing?
The auger size needed is dependant on the post size being installed, and the soil conditions you will be working in.
For a standard wooden fence, you may only require a 150mm (6”) or 200mm (8”) diameter auger. These sizes are large enough to accommodate most standard fence posts and provide a stable base for the fence.
If you are installing a chain-link or steel fence, you may want to consider a larger diameter auger, such as a 250mm (10”) or 300mm (12”) diameter. These larger sizes will provide a more stable base for the heavier fence posts and will also make it easier to accommodate larger posts if necessary. Typically, a rural fence using post and rail will use a 300mm (12”) for the post and a 450 (18”) up to 600mm(24”) for the corner or Strainer post.
It's also important to consider the length of the auger, which can range from 900mm (36”) to 1.5m (60”) or more. The length of the auger will depend on the depth of the hole you need to dig and will also be influenced by the soil conditions and the type of fence you are installing.
It's important to consult the fence manufacturers for specifications before deciding. *Always refer to local engineering and building codes for regulations and guidance.
Additionally, consider the power of your equipment and the capacity of your equipment to handle the auger size you choose.
What sets Digga augers apart from the competition?
Digga specialises in manufacturing augers and other attachments for construction and agriculture equipment.
The Digga Auger range has been developed over many years of working directly with our customers along with advanced engineering processes to perfect and optimise our cutting systems to provide the best performance possible, our augers are industry leading for several reasons, such as:
Quality: Digga augers are made with high-quality materials and built to last. We also have strict ISO90001 quality control procedures in place to ensure that each auger meets our standards.
Innovation: Digga have patented features or designs that set their augers apart from those of their competitors. we also invest heavily in research and development to ensure that our products are constantly improving.
Design: Digga’s highly skilled and professional engineering team utilising advanced 3D modelling to ensure the tooth angle and positioning is in the ideal position and angle to give the best cut and penetration ability, and ensure optimum flight pitch to both hold the spoil on the flight for better extraction while getting that spoil to the top of the hole quickly to help avoid auger stall.
Support: At Digga we pride ourselves on our strong customer service and technical support team that can assist customers with any questions or issues they may have with their augers. We offer assistance with choosing the right drilling tool option for your needs.
Versatility: Digga has a wide range of standard augers available together with Bespoke (custom) option to suit different types of projects, jobs, and machinery, coupled with an extensive range of accessories available to expand the capabilities of the auger and auger drive.
Brand reputation: Digga has a strong reputation in the industry for producing high-quality, reliable augers that are known for getting the job done.
It's important to note that different augers are better suited for different tasks and that the best option for you will depend on your specific needs and preferences.
Consult with the sales team for available options and guidance to help you make the best decision.
Do you make custom augers?
Yes, we do, we offer many bespoke drilling solutions.
Consult with the sales team for available options and guidance to help you make the best decision.
When do I need to change my teeth / picks / How long will my teeth last?
The teeth could last 1 or 2 holes or last 100’s of holes, its all dependant on what material is being drilled. Tungsten Carbide teeth/pilots will always out last standard earth teeth/pilots.
The lifespan of an auger tooth depends on a variety of factors, including the type of material it is made from, the type of soil or rock it is used to drill through, and the frequency and intensity of use.
Carbide teeth are known to last longer than steel teeth, due to their high hardness and resistance to wear. A carbide tooth can last for several hundred hours of drilling, depending on the specific type of carbide and the conditions it is being used in.
Steel teeth are generally less durable than carbide teeth and typically wear out faster.
It's important to note that drilling through hard rock, clay or concrete will wear out the teeth faster than drilling through softer soils. Additionally, drilling frequently or for longer periods of time will also decrease the lifespan of the teeth.
Proper maintenance such as regular inspections and replacing worn teeth can also help prolong the lifespan of the auger.
Do you make custom augers?
Yes, we do, we offer many bespoke drilling solutions.
Consult with the sales team for available options and guidance to help you make the best decision.